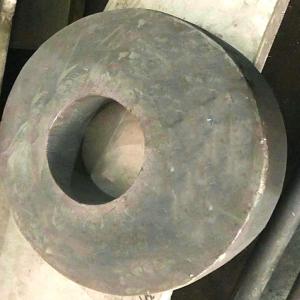
Add to Cart
Nickel Alloy Forged Shaft 430 Forging Rings Stainless Steel Shafting 304
1. Introduction
The production process
1. Raw materials:
According to the customer's drawings and material requirements, select the appropriate raw material grade and specification.
2. Steel testing:
In order to ensure the quality of raw materials, the chemical composition of raw materials shall be rechecked before production.
3, steel line blanking:
Cut steel ingot and billet into reasonable size and weight according to product requirements.
4. Heating (including tempering) :
Heat the cut raw materials according to the product process to ensure that the heating temperature meets the material requirements.
5. Forging:
By the manipulator into the forging equipment, according to the size of raw materials and forging ratio requirements for the corresponding pier thickness, drawing length and other processes, real-time monitoring of forging size, and through the infrared thermometer to control the forging temperature.
6. Forging inspection:
Conduct preliminary inspection of forging blanks, mainly the inspection of appearance and size. In terms of appearance, the main inspection is whether there are cracks and other defects. In terms of size, we must ensure that the blank allowance is within the range required by the drawing and make a good record.
7. Heat preservation normalizing after forging:
It is mainly to refine grain, uniform structure and eliminate internal stress. Improve defects: Weisite, coarse grain and other overheating defects and banded structure! Prepare for final heat treatment.
8, rough processing:
Forgings basic forming according to product demand processing of various specifications of forgings, with finishing allowance.
9. Heat treatment:
An integrated process of heating forgings to a predetermined temperature, holding them for a certain amount of time, and then cooling them at a predetermined rate to improve the internal organization and properties of forgings. Its purpose is to eliminate internal stress, prevent deformation during machining, adjust the hardness to make the forging conducive to cutting. After heat treatment of the forging, according to the requirements of the material of the forging, air cooling or water cooling, oil cooling, etc. Including: normalizing, tempering, quenching and other heat treatment.
10. Finishing:
After rough processing and heat treatment, the products are precision machined by CNC machine tools, so that the dimensional accuracy and finish of products fully meet the requirements of forging drawings.
11. Product appearance inspection:
Product appearance inspection in accordance with the customer's drawing size requirements. Carry out ultrasonic flaw detection (UT), magnetic particle flaw detection (MT), hardness, carburizing and other drawings.
12, mechanical performance test:
In order to meet customer needs, it is necessary to test the mechanical properties of forgings, mainly including yield, tensile, impact and metallographic tests. Meet the needs of various forgings testing.
13. Surface treatment and packaging:
After quality inspection, the finished forgings are processed with anti-rust paint and put into the finished goods warehouse for delivery.
14. Loading and delivery:
Pull merchandise out of the finished product warehouse ready to be loaded and shipped to customers.
Can process all kinds of: carbon steel, alloy steel, stainless steel
2. Product Show